Introducing DC Sputtering Systems and The Process
Sputtering is a process used to deposit thin films onto a substrate. It involves using a plasma generated from an inert process gas to eject sputtered material from a target surface. These emitted particles then form a vapour that will eventually condense onto the substrate and form a thin, even film.
DC sputtering, or direct current sputtering, is a thin film physical vapour deposition coating technique that uses a direct current as a power source. It offers numerous advantages in metal deposition for coating. DC sputtering is used extensively in manufacturing, such as adding metal layers to packaging materials, creating metallic finishes on watches and jewellery, and producing durable coatings on medical devices.
This guide will provide a comprehensive overview of DC sputtering, how it works, and its distinction from RF sputtering.
What Is DC Sputtering?
DC sputtering is a thin film deposition technique that uses direct current (DC) for depositing films from electrically conductive target materials onto a substrate. It is primarily used for applying metal coatings to surfaces and is favoured for its low cost, efficiency, and ability to create high-quality, uniform thin films when working with electrically conductive materials.
DC magnetron sputtering uses magnets behind the target to help trap positively charged ions near the target surface. The process takes place in a vacuum chamber, to help remove contaminants that will interfere with the generated film. Inside the chamber, a high-purity inert gas, typically argon, is introduced. When exposed to a DC or pulsed-DC current, this gas becomes ionised, enabling the sputtering process to occur.
The metal target material acts as the negative pole (cathode), while the substrate functions as the positive pole (anode). When a DC electrical current is applied to the target, it ionises the argon gas, causing the ions to collide forcefully with the negatively charged target material.
These high-energy molecular collisions knock off metal ions from the surface of the target, releasing them into the plasma (a mixture of ionised argon gas atoms and electrons). The substrate (now the anode) is in the path of the vapour flux generated from the target and so the vapour will condense onto the surface forming a thin film coating of the target material.
While DC sputtering is highly effective for conductive metals, it is less suitable for dielectric target materials. These materials can accumulate charge, which leads to arcing and disturbances in electron flow, causing an uneven deposition rate. The accumulation of positive ions can even cause the entire sputtering pathway to cease functioning, resulting in the need for a reset.
Check a breakdown of this deposition technique below.
How Does DC Sputtering Work?
Like any type of sputtering deposition method, the DC magnetron sputtering process requires a vacuum chamber. It also requires DC power, positively charged sputtering gas atoms, a target material, and a substrate.
Here is how DC magnetron sputtering systems deposit metal coatings onto substrates:
- The target or coating material to be used as the thin film is placed in a vacuum chamber.
- The vacuum chamber is positioned parallel to the desired substrate.
- The vacuum chamber removes water, air, hydrogen, and argon with a chamber pressure between 1 and 100 mTorr.
- The chamber then fills with an inert process gas, such as argon.
- The system applies a DC voltage to the target surface.
- The target coating material becomes the cathode, and the substrate becomes the anode.
- The neutral argon atoms become ionised when they collide with the negatively charged target and then eject into high-density plasma, which is generated through neutralisation.
- The now-ionised gas ions remain in the vacuum and break out the target atoms.
- The ionised gas molecules are driven to the substrate.
- The positive ions condense and form thin films on the substrate.
- The magnetic field traps electrons over the sputtering targets, preventing ion bombardment and allowing for faster deposition rates.
Overall, DC magnetron sputtering is a relatively simple technique with a high deposition rate, allowing manufacturers to deposit large quantities of surface materials onto substrates quickly, economically, and effectively. This process is essential in a range of commercial applications, such as depositing films of ZnO on glass substrates.
Korvus’s HEX series has the power and specialised mechanisms to deploy DC sputtering depositions. Additionally, combining the HEX series with the Fission DC/RF sputtering series module allows users to alternate between DC and RF sputtering without downtime or specialised equipment through a flow switch.
DC vs. RF Sputtering
There are different types of magnetron sputtering systems. Direct current sputtering and radio frequency sputtering or RF magnetron sputtering are two of them.
The primary distinguishers between these two processes are in their power source and applications.
What Is RF Sputtering?
Radio frequency (RF) sputtering is a type of sputtering for PVD with a process that aims to eliminate the charge buildup that can occur with certain target materials, such as in DC sputtering. This unwanted charge accumulation can disrupt the sputtering process and lead to quality control issues during film formation.
RF sputtering involves two processes: the ionisation of the sputtering gas and the sputtering of material from the target onto the substrate. This method alternates the potential of the current in the vacuum environment by using a high-voltage RF source. This alternating current avoids the buildup of charged plasma particles and gas ionisation, essentially “cleaning up” the charge buildup after every cycle.
If the first cycle uses a negatively charged target material, the ionised gas particles remain at the anode at the end of the cycle to maintain a stable environment for deposition. Then, the next cycle uses reverse polarisation to switch the charge on the target and substrate, resulting in positively charged sputtering gas atoms that move towards the negatively charged substrate.
The main drawback of RF sputtering is its low deposition rates compared to pulsed DC sputtering and a much higher power requirement. While the deposition rate can be improved by applying a strong magnetic field along the power source to keep the charged plasma discharge closer to the target surface, RF sputtering still requires more power. This is why most RF power supplies are designed to provide up to 1,000 V to generate the necessary signal for the sputtering process.
Another drawback of RF sputtering is the need for an impedance-matching network between the vacuum chamber and the RF power supply equipment. This network prevents interference from the RF discharge which may reduce the overall sputtering rate.
Most RF sputtering processes operate at a frequency of 13.5 MHz, with power supplies typically providing between 300 W and 1,000 W to generate this frequency. This range of power ensures that the RF signal is strong enough to create the necessary plasma for effective sputtering.
The Difference Between DC Sputtering and RF Sputtering
Although DC and RF sputtering are both widely used deposition methods, these processes impact the material morphology of their sputtering targets differently.
One of the main differences between DC and RF sputtering is the type of power used. DC sputtering uses a direct current, whereas RF sputtering alternates the electrical charge to prevent charge accumulation on the target material. Due to the alternating current in RF power supplies, RF sputtering is sometimes called AC sputtering.
RF sputtering deposition rates are slower than DC sputtering rates.
While DC sputtering is suitable for depositing large quantities onto large substrates, RF is more effective within smaller substrates.
Moreover, DC and RF sputtering can be used to deposit different types of target materials. DC sputtering is limited to electrically conductive materials, whereas RF sputtering can deposit both conductive and non-conductive target materials.
Finally, DC and RF sputtering vary in complexities and price points. DC sputtering is generally more affordable due to its simpler process, while the RF sputtering method is pricier due to its intricate process, though its versatility and excellent campaign length make up for its high price point.
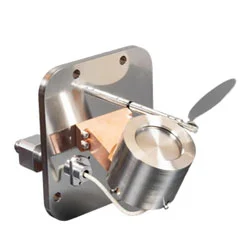
The Advantages of DC Sputtering for Thin Film Manufacturing
DC sputtering is the most basic and inexpensive type of PVD metal deposition method, due to the relative simplicity of the DC power used in the process. It offers numerous advantages over RF sputter deposition within thin-film manufacturing.
DC magnetron sputtering allows manufacturing companies to benefit from reduced equipment and process costs, leading to better profit margins. The basic configuration of a DC sputtering system is simple, which continues to make DC sputtering the low-cost solution compared to other methods of sputter deposition. Moreover, this process can be adapted for magnetic sputtering targets, such as iron, nickel, and cobalt.
DC magnetron sputter deposition is also easy to control, offering greater precision and flexibility within the manufacturing process. Using DC as a power source allows for more versatility in the chamber pressure vacuum, which makes this process applicable to numerous thin-film deposition materials.
Additionally, the DC magnetron sputtering allows for higher current, resulting in an impressive sputtering rate compared to other methods. This advantage allows DC sputtering systems to process large substrates quickly.
However, there are some limitations of DC sputtering. As mentioned earlier, it is only suitable for conductive materials. When used to deposit non-conductive insulating materials, the materials may accumulate an electric charge, which can harm the target material.
Notably, this limitation is overcome by other sputtering processes for deposited films, such as radio frequency sputtering and reactive sputtering.
Final Thoughts
Altogether, DC magnetron sputtering is a highly advantageous physical vapour deposition technique for depositing thin layers of films onto conductive substrates. This process offers benefits in terms of complexity and affordability, making it suitable for a range of commercial applications, especially when considering the DC power source compared to the RF power source.
If you’re interested in implementing DC sputtering within your lab or research facility, we can help. Our Fission DC and RF Sputtering System supports sputtering processes for a range of materials, including all solid metals. This system even supports high-power impulse magnetron sputtering (HiPIMS) and Pulse-DC power.
Contact us today to learn more about the Fission module of the HEX Sputtering System.
References
[1] Banerjee, A.N. et al. (2005). “Low-temperature deposition of ZnO thin films on PET and glass substrates by DC-sputtering technique.” Thin Solid Films, 496(1), 112-116.
[2] T Bui, Mathieu Halbwax, Jean-Pierre Vilcot. (2021). “Comparison of DC and RF Sputtering of ZnSnN2 : Effect on Structural, Optical and Electrical Properties.” Journées Nationales du PhotoVoltaïque, Fédération de recherche du PhotoVoltaïque, FedPV.
[3] Kim, Jaemin et al. (2020). “Effect of IGZO thin films fabricated by Pulsed-DC and RF sputtering on TFT characteristics.” Materials Science in Semiconductor Processing, 120.