The Uses of Thin Film Coating in the Medical Industry
Thin film coatings have applications across a multitude of industries, ranging from aerospace to energy. Thin films are also an integral part of biomedical applications, including glass, metal, and plastic surfaces of medical devices.
This article explores how the mechanical properties of thin film coatings benefit the life sciences, including thin film coatings in implants, drug delivery systems, and surgical instruments.
Why Are Thin Film Coatings Used in the Medical Industry?
The medical industry continues to advance, and new technologies constantly emerge that allow doctors and scientists to achieve breakthroughs. From advanced laser surgical processes to biomaterials that function as implants or replacement parts, there is a need to ensure that any material introduced to the human body is safe, comfortable, and durable.
Medical devices (including implants and surgical tools) require thin film coatings to function adequately and protect the body from harm. The benefits of thin films for medical industries include:
- Enhanced biocompatibility: Ability of the body to accept the foreign material
- Wear resistance: A measure of durability, scratch resistance and comfort
- Corrosion resistance: Devices must resist corroding or breaking down when introduced to bodily fluids and tissue
- Reduced friction: Comfort is critical
- Improved surface properties: Thin film optical coatings and polymer coatings embody the benefits of reduced friction, durability, and comfort, enabling surface modification for low surface roughness, especially when composed of indium tin oxide.
Thin Film Coatings in Implants
Early technology in the area of implants was woefully inadequate due to poor biocompatibility and low levels of strength. As stainless steel and other metal materials were utilised, the biocompatibility and degradation issues remained to be solved.
Over time, companies like DuPont began the development of other materials and processes, including thin films. For example, diamond-like carbon coatings (DLC) are thin films that serve as protecting coatings and are much more comfortable in biological settings.
Employing a physical vapour deposition (PVD) system allowed DLC coatings to be more flexible and meet the exacting standards of the medical device industry.
As demand continues to rise, there’s also a need for high-volume manufacturing. Magnetron sputtering systems can achieve this by producing thin films that accomplish both bulk production and the need for better performance in the following areas:
- Enhanced biocompatibility: Thin films are less intrusive so function better in the body.
- Improved wear resistance: The deposition process equips an implant and optical surface to resist wear, so reduce the chance of deterioration within the body.
- Improved osseointegration: This process involves the fusing of the implant to the body’s internal structure or tissue. Sputtering within predefined process parameters has led to good adhesion and overall high success rates.
- Reduced infection rates: The chemical composition and antibacterial properties of the coatings deposited, and the high temperatures serve to prevent the formation and promulgation of bacteria.
Uses of Thin Film Coatings in Drug Delivery Systems
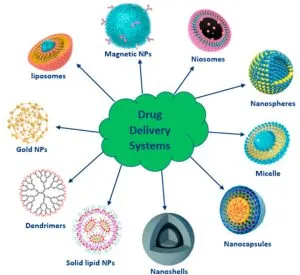
Thin films are also being used by pharmaceutical scientists as a drug delivery tool through multiple biological systems. With this coating technology, the following benefits have been attained:
- Improved drug release (improved onset and efficacy)
- Enhanced drug stability
- Controlled release (ideal for delayed release
- Reduced side effects
Applying thin films to the surfaces of surgical tools like blades has been shown to enhance cutting properties while decreasing the risk of post-surgical complications. Similar to the benefits of implants and drug delivery systems, thin film coatings on surgical instruments are expected to provide the following benefits:
- Improved biocompatibility
- Enhanced durability and wear resistance
- Reduced friction
- Corrosion resistance
These benefits have been proven and measured by scanning the optical properties of glass and other surfaces using scanning electron microscopy and atomic force microscopy to calculate surface roughness, friction, and other success indicators.
The Future of Medical Industry Thin Film Coating
As advancements in technology are expected to continue, there is massive potential for new applications in the medical industry. These technological advancements will continue to provide new benefits for patients and the healthcare industry by improving outcomes, extending longevity, and improving quality of life.
While the advent and adoption of nanotechnology, the exceedingly small surfaces and minute thickness of devices will increasingly rely on the use and continued evolution of thin film coatings. Contact Korvus to learn more about our thin film deposition system and how it can help with your medical thin film research.
References
[1] Medical and Biomedical Thin Film Materials: Prosthetic Implants, Materion Technical Paper
[2] Shivashish Kulshreshtha, Applications of Thin Film Technology for Medical Implants, National Institute of Technology Calicut (June, 2020)
[3] Ihab Nabeel Safi, et al. (2021), Effects of Long Durations of RF-Magnetron Sputtering Deposition of Hydroxyapatite on Titanium Dental Implants, Eur J Dent. 440-447. DOI: 10.1055/s-0040-1721314.
[4] Sandeep Karki, et al. (2016) Thin films as an emerging platform for drug delivery, Asian Journal of Pharmaceutical Sciences, Volume 11, Issue 5, Pages 559-574
[5] Magdalena Szindler, et al. (2021) Application of ALD Thin Films on the Surface of the Surgical Scalpel Blade, Coatings, 11(9), 1096